Inverter Fed Induction Motor Drives
Induction motor can only run efficiently at low slips, i.e. close to the synchronous speed of the rotating field. The best method of speed control must therefore provide for continuous smooth variation of the synchronous speed, which in turn calls for variation of the supply frequency. This is achieved using an inverter to supply the motor.
A complete speed control scheme which includes tacho (speed) feedback is shown in block diagram Figure 1.
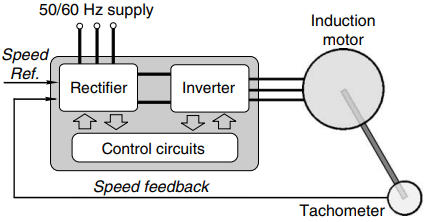
We should recall that the function of the converter (i.e. rectifier and variable-frequency inverter) is to draw power from the fixed-frequency constant-voltage mains, and convert it to variable frequency, variable voltage for driving the induction motor. Both the rectifier and the inverter employ switching strategies, so the power conversions are accomplished efficiently and the converter can be compact.
Variable frequency inverter-fed induction motor drives are used in ratings up to hundreds of kilowatts. Standard 50 Hz or 60 Hz motors are often used (though as we will see later this limits performance), and the inverter output frequency typically covers the range from around 5–10 Hz up to perhaps 120 Hz. This is sufficient to give at least a 10:1 speed range with a top speed of twice the normal (mains frequency) operating speed.
The majority of inverters are 3-phase input and 3-phase output, but single-phase input versions are available up to about 5 kW, and some very small inverters (usually less than 1 kW) are specifically intended for use with single-phase motors.
A fundamental aspect of any converter, which is often overlooked, is the instantaneous energy balance. In principle, for any balanced three-phase load, the total load power remains constant from instant to instant, so if it was possible to build an ideal 3-phase input, 3-phase output converter, there would be no need for the converter to include any energy storage elements.
In practice, all converters require some energy storage (in capacitors or inductors), but these are relatively small when the input is 3-phase because the energy balance is good.
However, as mentioned above, many small and medium power converters are supplied from single-phase mains. In this case, the instantaneous input power is zero at least twice per cycle of the mains (because the voltage and current go through zero every half-cycle).
If the motor is 3-phase (and thus draws power at a constant rate), it is obviously necessary to store sufficient energy in the converter to supply the motor during the brief intervals when the load power is greater than the input power. This explains why the most bulky components in many small and medium power inverters are electrolytic capacitors.
The majority of inverters used in motor drives are voltage source inverters (VSI), in which the output voltage to the motor is controlled to suit the operating conditions of the motor. Current source inverters (CSI) are still used, particularly for large applications, but will not be discussed here.
Comparison with D.C. Drive
The initial success of the inverter-fed induction motor drive was due to the fact that a standard induction motor was much cheaper than a comparable d.c. motor, and this saving compensated for the relatively high cost of the inverter compared with the thyristor d.c. converter.
But whereas a d.c. drive was invariably supplied with a motor provided with laminated field poles and through ventilation to allow it to operate continuously at low speeds without overheating, the standard induction motor has no such provision, having been designed primarily for fixed-frequency full-speed operation.
Thus, although the inverter is capable of driving the induction motor with full torque at low speeds, continuous operation is unlikely to be possible because the cooling fan will be ineffective and the motor will overheat.
Now that inverter-fed drives dominate the market, two changes have become evident. Firstly, reputable suppliers now warn of the low-speed limitation of the standard induction motor, and encourage users to opt for a blower-cooled motor if necessary. And secondly, the fact that inverter-fed motors are not required to start direct-on-line at supply frequency means that the design need no longer be a compromise between starting and running performance.
Motors can therefore be designed specifically for operation from an inverter, and have low-resistance cages giving very high steady-state efficiency and good open-loop speed holding. The majority of drives do still use standard motors, but inverter-specific motors with integral blowers are gradually gaining ground.
The steady-state performance of inverter-fed drives is broadly comparable with that of d.c. drives (except for the limitation highlighted above), with drives of the same rating having similar overall efficiencies and overall torque–speed capabilities. Speed holding is likely to be less good in the induction motor drive, though if tacho feedback is used both systems will be excellent.
The induction motor is clearly more robust and better suited to hazardous environments, and can run at higher speeds than the d.c. motor, which is limited by the performance of its commutator.
Some of the early inverters did not employ pulse width modulation (PWM), and produced jerky rotation at low speed. They were also noticeably more noisy than their d.c. counterparts, but the widespread adoption of PWM has greatly improved these aspects.
Most low and medium power inverters use MOSFET or IGBT devices, and may modulate at ultrasonic frequencies, which naturally result in relatively quiet operation. The Achilles heel of the basic inverter-fed system has been the relatively poor transient performance. For fan and pump applications and high-inertia loads this is not a serious drawback, but where rapid response to changes in speed or load is called for (e.g. in machine tools or rolling mills), the d.c. drive with its fast-acting current-control loop traditionally proved superior.
However, it is now possible to achieve equivalent levels of dynamic performance from induction motors, but the complexity of the control naturally reflects in a higher price.
Most manufacturers now offer this so-called ‘vector’ or ‘field-oriented’ control as an optional extra for high-performance drives.
Inverter Waveforms
When we looked at the converter-fed d.c. motor we saw that the behaviour was governed primarily by the mean d.c. voltage, and that for most purposes we could safely ignore the ripple components. A similar approximation is useful when looking at how the inverter-fed induction motor performs. We make use of the fact that although the actual voltage waveform supplied by the inverter will not be sinusoidal, the motor behaviour depends principally on the fundamental (sinusoidal) component of the applied voltage.
This is a somewhat surprising but extremely welcome simplification, because it allows us to make use of our knowledge of how the induction motor behaves with a sinusoidal supply to anticipate how it will behave when fed from an inverter.
In essence, the reason why the harmonic components of the applied voltage are much less significant than the fundamental is that the impedance of the motor at the harmonic frequencies is much higher than at the fundamental frequency. This causes the current to be much more sinusoidal than the voltage, as shown in Figure 2, and this in turn means that we can expect a sinusoidal travelling field to be set up.
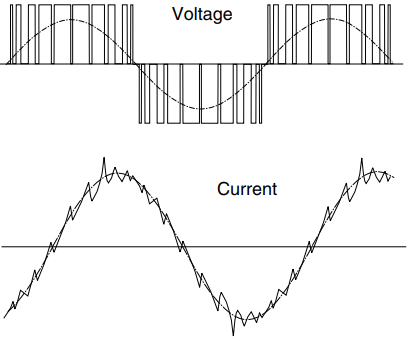
It would be wrong to pretend that the harmonic components have no effects, of course. They can create unpleasant acoustic noise, and always give rise to additional iron and copper losses. As a result it is common for a standard motor to have to be de-rated (by up to perhaps 5 or 10%) for use on an inverter supply.
As with the d.c. drive the inverter-fed induction motor drive will draw non-sinusoidal currents from the utility supply. If the supply impedance is relatively high significant distortion of the mains voltage waveform is inevitable unless filters are fitted on the a.c. input side, but with normal industrial supplies there is no problem for small inverters of a few kW rating.
Some inverters now include ‘front-end conditioning’ i.e. an extra high-frequency switching stage and filter which ensure that the current drawn from the mains is not only sinusoidal, but also at unity power factor. This feature will become widespread in medium and high power drives to meet the increasingly stringent conditions imposed by the supply authorities.
Steady State Operation – Importance of Achieving Full Flux
Three simple relationships need to be borne in mind to simplify understanding of how the inverter-fed induction motor behaves. Firstly, for a given induction motor, the torque developed depends on the strength of the rotating flux density wave, and on the slip speed of the rotor, i.e. on the relative velocity of the rotor with respect to the flux wave.
Secondly, the strength or amplitude of the flux wave depends directly on the supply voltage to the stator windings, and inversely on the supply frequency. And thirdly, the absolute speed of the flux wave depends directly on the supply frequency.
Recalling that the motor can only operate efficiently when the slip is small, we see that the basic method of speed control rests on the control of the speed of rotation of the flux wave (i.e. the synchronous speed), by control of the supply frequency. If the motor is a 4-pole one, for example, the synchronous speed will be 1500 rev/min when supplied at 50 Hz, 1200 rev/min at 40 Hz, 750 rev/min at 25 Hz and so on.
The no-load speed will therefore be almost exactly proportional to the supply frequency, because the torque at no load is small and the corresponding slip is also very small.
Turning now to what happens on load, we know that when a load is applied the rotor slows down, the slip increases, more current is induced in the rotor, and more torque is produced. When the speed has reduced to the point where the motor torque equals the load torque, the speed becomes steady.
We normally want the drop in speed with load to be as small as possible, not only to minimise the drop in speed with load, but also to maximise efficiency: in short, we want to minimise the slip for a given load.
The slip for a given torque depends on the amplitude of the rotating flux wave: the higher the flux, the smaller the slip needed for a given torque. It follows that having set the desired speed of rotation of the flux wave by controlling the output frequency of the inverter we must also ensure that the magnitude of the flux is adjusted so that it is at its full (rated) value, regardless of the speed of rotation. This is achieved by making the output voltage from the inverter vary in the appropriate way in relation to the frequency.
We recall that the amplitude of the flux wave is proportional to the supply voltage and inversely proportional to the frequency, so if we arrange that the voltage supplied by the inverter vary in direct proportion to the frequency, the flux wave will have a constant amplitude.
This philosophy is at the heart of most inverter-fed drive systems: there are variations, as we will see, but in the majority of cases the internal control of the inverter will be designed so that the output voltage to frequency ratio (V/f ) is automatically kept constant, at least up to the ‘base’ (50 Hz or 60 Hz) frequency.
Many inverters are designed for direct connection to the mains supply, without a transformer, and as a result the maximum inverter output voltage is limited to a value similar to that of the mains. With a 415 V supply, for example, the maximum inverter output voltage will be perhaps 450 V.
Since the inverter will normally be used to supply a standard induction motor designed for say 415 V, 50 Hz operation, it is obvious that when the inverter is set to deliver 50 Hz, the voltage should be 415 V, which is within the inverter’s voltage range.
But when the frequency was raised to say 100 Hz, the voltage should – ideally – be increased to 830 V in order to obtain full flux. The inverter cannot supply voltages above 450 V, and it follows that in this case full flux can only be maintained up to speeds a little above base speed. (It should be noted that even if the inverter could provide higher voltages, they could not be applied to a standard motor because the winding insulation will have been designed to withstand not more than the rated voltage.)
Established practice is for the inverter to be capable of maintaining the V/f ratio constant up to the base speed (50 Hz or 60 Hz), but to accept that at all higher frequencies the voltage will be constant at its maximum value. This means that the flux is maintained constant at speeds up to base speed, but beyond that the flux reduces inversely with frequency. Needless to say the performance above base speed is adversely affected, as we will see. Users are sometimes alarmed to discover that both voltage and frequency change when a new speed is demanded.
Particular concern is expressed when the voltage is seen to reduce when a lower speed is called for. Surely, it is argued, it can’t be right to operate say a 400 V induction motor at anything less than 400 V. The fallacy in this view should now be apparent: the figure of 400 V is simply the correct voltage for the motor when run directly from the mains, at say 50 Hz.
If this full voltage was applied when the frequency was reduced to say 25 Hz, the implication would be that the flux would have to rise to twice its rated value. This would greatly overload the magnetic circuit of the machine, giving rise to excessive saturation of the iron, an enormous magnetising current and wholly unacceptable iron and copper losses.
To prevent this from happening, and keep the flux at its rated value, it is essential to reduce the voltage in proportion to frequency. In the case above, for example, the correct voltage at 25 Hz would be 200 V.
TORQUE–SPEED CHARACTERISTICS – CONSTANT V/F OPERATION
When the voltage at each frequency is adjusted so that the ratio V/f is kept constant up to base speed, and full voltage is applied thereafter, a family of torque–speed curves as shown in Figure 3 is obtained. These curves are typical for a standard induction motor of several kW output.
As expected, the no-load speeds are directly proportional to the frequency, and if the frequency is held constant, e.g. at 25 Hz in Figure 3, the speed drops only modestly from no-load (point a) to full-load (point b).
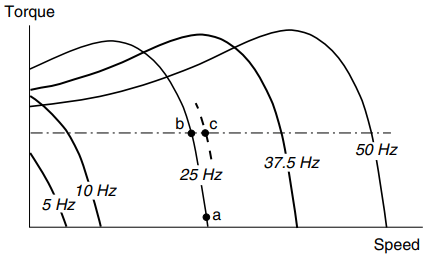
These are therefore good open-loop characteristics, because the speed is held fairly well from no-load to full-load. If the application calls for the speed to be held precisely, this can clearly be achieved (with the aid of closed-loop speed control) by raising the frequency so that the full-load operating point moves to point (c).
We also note that the pull-out torque and the torque stiffness (i.e. the slope of the torque–speed curve in the normal operating region) is more or less the same at all points below base speed, except at low frequencies where the effect of stator resistance in reducing the flux becomes very pronounced.
It is clear from Figure 3 that the starting torque at the minimum frequency is much less than the pullout torque at higher frequencies, and this could be a problem for loads which require a high starting torque.
The low-frequency performance can be improved by increasing the V/f ratio at low frequencies in order to restore full flux, a technique which is referred to as ‘low-speed voltage boosting’.
Most drives incorporate provision for some form of voltage boost, either by way of a single adjustment to allow the user to set the desired starting torque, or by means of more complex provision for varying the V/f ratio over a range of frequencies.
A typical set of torque–speed curves for a drive with the improved low-speed torque characteristics obtained with voltage boost is shown in Figure 4. The curves in Figure 4 have an obvious appeal because they indicate that the motor is capable of producing practically the same maximum torque at all speeds from zero up to the base (50 Hz or 60 Hz) speed.
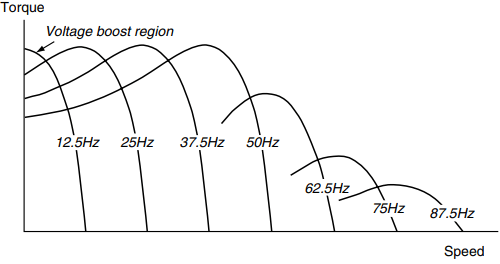
This region of the characteristics is known as the ‘constant torque’ region, which means that for frequencies up to base speed, the maximum possible torque which the motor can deliver is independent of the set speed. Continuous operation at peak torque will not be allowable because the motor will overheat, so an upper limit will be imposed by the controller, as discussed shortly.
With this imposed limit, operation below base speed corresponds to the armature-voltage control region of a d.c. drive. We should note that the availability of high torque at low speeds (especially at zero speed) means that we can avoid all the ‘starting’ problems associated with fixed-frequency operation.
By starting off with a low frequency which is then gradually raised the slip speed of the rotor is always small, i.e. the rotor operates in the optimum condition for torque production all the time, thereby avoiding all the disadvantages of high-slip (low torque and high current) that are associated with mains-frequency starting.
This means that not only can the inverter-fed motor provide rated torque at low speeds, but – perhaps more importantly – it does so without drawing any more current from the mains than under full-load conditions, which means that we can safely operate from a weak supply without causing excessive voltage dips.
For some essentially fixed-speed applications, the superior starting ability of the inverter-fed system alone may justify its cost. Beyond the base frequency, the V/f ratio reduces because V remains constant. The amplitude of the flux wave therefore reduces inversely with the frequency.
The pull-out torque always occurs at the same absolute value of slip speed, and that the peak torque is proportional to the square of the flux density. Hence in the constant voltage region the peak torque reduces inversely with the square of the frequency and the torque–speed curve becomes less steep, as shown in Figure 4.
Although the curves in Figure 4 show what torque the motor can produce for each frequency and speed, they give no indication of whether continuous operation is possible at each point, yet this matter is of course extremely important from the user’s viewpoint, and is discussed next.
Limitations Imposed by Inverter – Constant Power and Constant Torque Regions
The main concern in the inverter is to limit the currents to a safe value as far as the main switching devices are concerned. The current limit will be at least equal to the rated current of the motor, and the inverter control circuits will be arranged so that no matter what the user does the output current cannot exceed a safe value. The current limit feature imposes an upper limit on the permissible torque in the region below base speed.
This will normally correspond to the rated torque of the motor, which is typically about half the pull-out torque, as indicated by the shaded region in Figure 5. In the region below base speed, the motor can therefore develop any torque up to rated value at any speed (but not necessarily for prolonged periods, as discussed below). This region is therefore known as the ‘constant torque’ region, and it corresponds to the armature voltage control region of a d.c. drive.
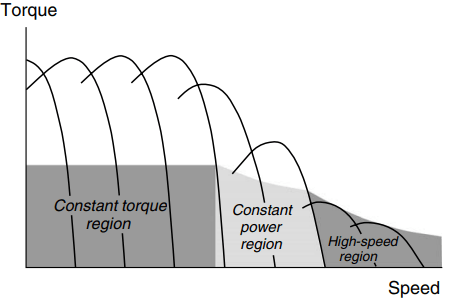
Above base speed of the flux is reduced inversely with the frequency; because the stator (and therefore rotor) currents are limited, the maximum permissible torque also reduces inversely with the speed, as shown in Figure 5. This region is therefore known as the ‘constant power’ region.
There is of course a close parallel with the d.c. drive here, both systems operating with reduced or weak field in the constant power region. The region of constant power normally extends to somewhere around twice base speed, and because the flux is reduced the motor has to operate with higher slips than below base speed to develop the full rotor current and torque. At the upper limit of the constant power region, the current limit coincides with the pull-out torque limit.
Operation at still higher speeds is sometimes provided, but constant power is no longer available because the maximum torque is limited to the pull-out value, which reduces inversely with the square of the frequency. In this high-speed motoring region (Figure 5), the limiting torque–speed relationship is similar to that of a series d.c. motor.
Limitations Imposed by Motor
The standard practice in d.c. drives is to use a motor specifically designed for operation from a thyristor converter. The motor will have a laminated frame, will probably come complete with a tachogenerator, and – most important of all – will have been designed for through ventilation and equipped with an auxiliary air blower. Adequate ventilation is guaranteed at all speeds, and continuous operation with full torque (i.e. full current) at even the lowest speed is therefore in order.
By contrast, it is still common for inverter-fed systems to use a standard industrial induction motor. These motors are totally enclosed, with an external shaft-mounted fan, which blows air over the finned outer case. They are designed first and foremost for continuous operation from the fixed frequency mains, and running at base speed.
When such a motor is operated at a low frequency (e.g. 10 Hz), the speed is much lower than base speed and the efficiency of the cooling fan is greatly reduced. At the lower speed, the motor will be able to produce as much torque as at base speed (see Figure 4) but in doing so the losses in both stator and rotor will also be more or less the same as at base speed.
Since the fan was only just adequate to prevent overheating at base speed, it is inevitable that the motor will overheat if operated at full torque and low speed for any length of time. Some suppliers of inverter drives do not emphasise this limitation, so users need to raise the question of whether a non-standard motor will be needed.
When through-ventilated motors with integral blowers become the accepted standard, the inverter-fed system will be freed of its low-speed limitations. Meanwhile users should note that one approach designed to combat the danger of motor overheating at low speeds is for the control circuits to be deliberately designed so that the flux and current limit are reduced at low speeds.
The constant-torque facility is thus sacrificed in order to reduce copper and iron losses, but as a result the drive is only suitable for fan- or pump-type loads, which do not require high torque at low speed. These systems inevitably compare badly with d.c. drives, but manage to save face by being promoted as ‘energy-saving’ drives.